A few days ago, the University of Michigan worked with Altair Engineering and Stratasys to form the CYBER team. The team recently commissioned and funded America Makes, a national innovation researcher for additive manufacturing , to develop a solution that will use 3D printing and Industry 4.0 to transform the ankle-foot orthosis ( AFO) design, comfort, usability and customization.
To do this, the CYBER team will develop a digital process for additive manufacturing (AM) design that will be connected to a cloud-based network system through which the fusion deposition (FDM) ?) Additive manufacturing technology and Altair OptiStructTM software to achieve customized manufacturing of ankle-foot orthosis (AFO).
Current pain points made by AFO
Traditionally, to customize AFO for a patient, skilled orthodontists and technicians are required to use a FRP cast strip to create an "impression" for the patient's lower leg (A and B, see figure below); And then casting a liquid gypsum into the cavity to create a model; (d) manually modifying the plaster model at the corresponding location of the patient's skeletal and pressure-resistant zones; (E) vacuum forming around the model using a thermoplastic plate; (f) Manually trim the plastic orthosis to the final shape; then add the necessary auxiliary materials, such as fillers or tapes, to it; and finally attach it to the AFO patient.
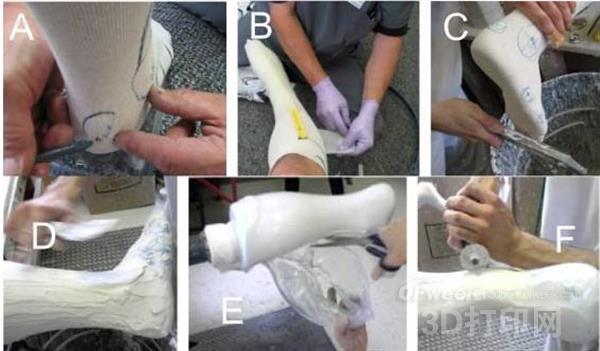
Traditional craftsmanship for making custom ankle-foot orthoses
The pain point of this process is that due to the need for many links and skilled technicians, the delivery cycle usually takes 2 to 4 weeks; and the process uses a large amount of disposable gypsum material; while the thickness of the plate used by the orthosis does not limit its optimization. The ability to structure and weight; in addition, it is not compatible with modern analytical techniques to optimize the strength and resilience of AFO to maximize patient mobility.
CYBER Solution: AFO Manufacturing via Industry 4.0
To this end, the CYBER team works together to directly address these pain points affecting patients and caregivers, while optimizing AFO, reducing manufacturing costs and speeding up production.
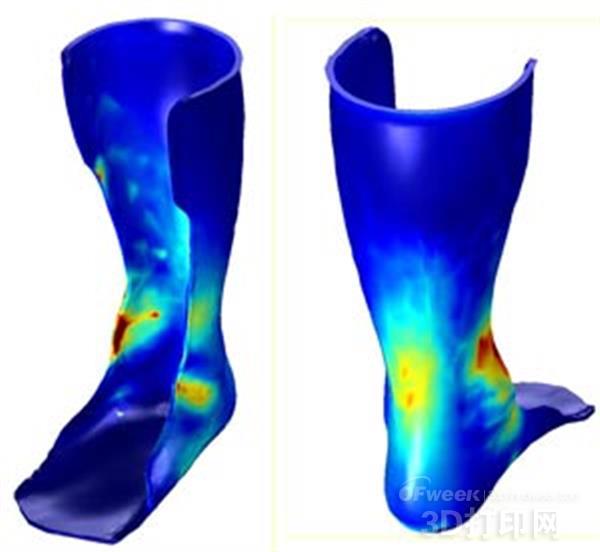
Future cloud-based network physics systems will allow clinicians to create AFOs using an online portal and combine their clinical expertise with automated tools to develop prescriptions for patients. The network physics system they developed will seamlessly integrate cloud-based algorithmic processes with physical component manufacturing to optimize the overall geometry of the component and its corresponding toolpath.
The advantages of this AFO additive manufacturing solution include:
Reduce delivery time: AFO usually delivers 2-4 weeks. The team plans to reduce delivery time to one day through a network physical system;
Increased accuracy: Gypsum tends to shrink after drying, so it is often difficult to accurately replicate the shape of the ankle and foot of a patient without an iterative or experienced practitioner. The CYBER team plans to provide an accurate, accurate AFO design with accurate 3D scanning.
Multiple visits were avoided: the patient completed the AFO manufacturing in one visit, saving the cost of patients and caregivers.
Increased freedom of AFO design: AFO's shape is limited by current manufacturing capabilities, making it impossible for physicians and designers to design more complex functions.
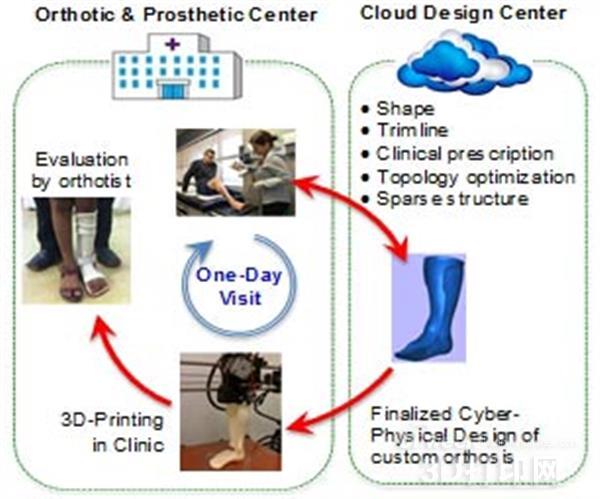
The team plans to drive future AFO designs through optimizations based on computational models and toolpaths, while encouraging clinicians to participate in providing personalized care. According to Tiangong, the average age of a lower limb orthosis user is 70 years old, so lightweight and ease of use are very important in this project.
However, for the time being, AFO's additive manufacturing process is quite complicated, and the requirements for operators are very high. In addition, the current additive manufacturing process has some shortcomings:
Machine manufacturing capabilities: The current manufacturing capabilities of additive manufacturing technology are not sufficient to support a patient's access to a customized AFO. CYBER needed to find a new design approach to increase machine capacity and achieve lower material usage while maintaining structural integrity and functionality.
Multi-Material: On a custom AFO, both rigid materials are required to provide structural functionality and flexible materials provide comfort;
Lack of clinical interface and system integration: There is currently no software system that can process all data seamlessly, including the patient's 3D scan size, orthosis shape, and 3D printed command files.
US veterans will take the lead
According to the CYBER team's plan, the US Veterans Administration (VA) will be the first partner of the solution. Once tested, the program will be deployed to VA orthoses and prosthetic outlets throughout the United States, primarily for veterans and their families.
According to statistics, from 2005 to 2009, VA spent almost 80% on orthotics and prosthetics, from $907 million to $1.6 billion. In 2009 alone, VA provided 1.5 million orthoses to veterans. This number is growing as the population ages. According to the American Society of Orthopaedic Prosthetics (AOPA), if the CYBER team's additive manufacturing solution can be fully deployed in the VA network, by 2020, each piece of medical insurance will save $1.3 billion.
The project is expected to complete proof of concept in 2017.